La réalité virtuelle optimise la production de l'usine Pringles, à Malines
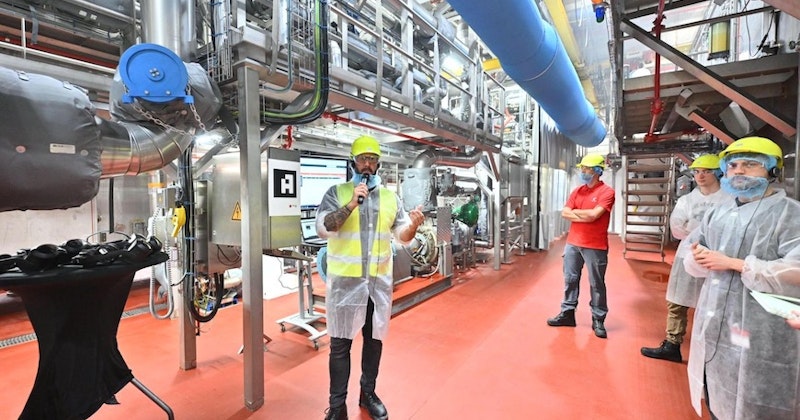
Pringles
L'usine Pringles de Malines fait appel à la réalité virtuelle pour optimiser le processus de production des Pringles et mieux former les employés. Pour ce faire, elle collabore avec plusieurs étudiants de Howest et avec l'entreprise Spectr BIM, spécialisée en technologie 3D.
6 mois, c'est le temps qu'il aura fallu pour mettre en place ce projet de réalité virtuelle. Kellanova, connue pour sa marque de chips Pringles, s'est associée à plusieurs étudiants de l'école supérieure Howest de Courtrai et à l'entreprise Spectr BIM, basée à Malines, spécialisée dans la technologie 3D. Concrètement, le projet consiste à utiliser la RV pour optimiser le processus de production et former plus facilement les travailleurs. "Le four doit rester à la même température en permanence. Si nous l'ouvrons pour surveiller le fonctionnement à l'intérieur, nous nous exposons à de graves pertes. Il fallait donc trouver une autre méthode de travail. En collaboration avec les équipes de Kellanova, les étudiants de Howest ont développé un système qui, pour la première fois, permet de visualiser la phase de cuisson dans la grande friteuse - une machine fermée. Grâce à cette visualisation interactive, la production peut être optimisée sans arrêter les activités de production. Il en résulte un gain de temps considérable, d'une part, et une optimisation de la consommation d'énergie, d'autre part. Cela nous permet également d'améliorer notre connaissance de l'intérieur des machines et de former plus facilement les employés", explique Tom De Weerdt, directeur principal des opérations techniques chez Kellanova. La visualisation est possible grâce à la technologie de Spectr BIM, qui représente les dessins CAO des machines à l'aide de la technologie 3D et y ajoute des animations, ce qui facilite la détection d'éventuels défauts. "Par exemple, si une vanne de la machine cesse de fonctionner, vous pouvez voir où se situe le problème grâce au flux d'huile sur les images de réalité virtuelle, ce qui nous permet de gagner beaucoup de temps pour détecter et résoudre le problème. Cela permet de réduire efficacement le gaspillage alimentaire et de préserver les ressources", poursuit-il. "Il est par ailleurs possible de simuler ces scénarios dans le système de RV, ce qui nous permet de mieux apprendre à gérer ces situations à l'avenir. Un autre avantage important du nouveau système est que l'outil de RV utilise des données réelles provenant des machines utilisées, ce qui permet d'analyser beaucoup mieux le processus de production."
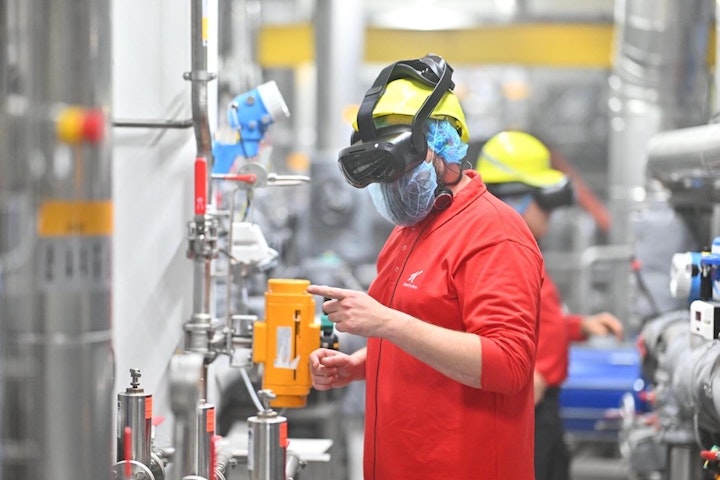
Pringles
Les premières réactions au système de RV sont déjà élogieuses, souligne M. De Weerdt. "Jusqu'à présent, aucune des usines de Kellanova ne travaillait avec la RV, mais nous constatons que notre projet est suivi de près par nos collègues des autres usines. Et qu'ils envisagent de déployer notre système dans d'autres usines de Kellanova également", déclare M. De Weerdt, qui souligne que la technologie de la RV offre encore beaucoup de potentiel à l'avenir. "Le système peut également être utilisé pour d'autres tâches telles que la maintenance critique ou les tâches opérationnelles, ainsi que pour la réalité mixte. Lode Snackaert, directeur général de Spectr BIM, ajoute : "Ce projet de RV est un projet industriel unique en Belgique car il utilise cette technologie d'une manière très innovante. Cette collaboration montre l'incroyable potentiel de la combinaison de l'innovation académique et de l'expertise industrielle pour révolutionner les processus de fabrication." Il souligne toutefois que la technologie 3D est encore sous-utilisée par les entreprises aujourd'hui : "Elles doivent vraiment aller au-delà de l'aspect agréable de la 3D et déployer cette technologie pour réaliser d'importantes économies dans leurs processus de production. Avec ce projet, Kellanova prouve que la technologie offre une valeur ajoutée significative".
Ce nouveau projet s'inscrit dans le cadre d'un investissement de plusieurs millions de Kellanova Europe visant à améliorer l'efficacité opérationnelle, à stimuler l'innovation au sein du réseau de production européen, mais aussi à réduire les déchets, les émissions de CO2 et la consommation d'eau dans l'ensemble du réseau de production. Ce n'est d'ailleurs pas la première fois que des améliorations durables sont apportées au site de l'usine Pringles Kellanova de Malines. L'usine, qui produit plus de 100 000 tonnes de snacks par an, a par exemple réussi à réduire sa consommation d'eau de 50 % cette année, en partie grâce à la construction d'une station de récupération des eaux usées en collaboration avec l'entreprise malinoise Pantarein. L'entreprise a également modifié l'an passé l'emballage de ses Pringles et a opté pour une base en papier, ce qui lui a permis d'améliorer le processus de recyclage.